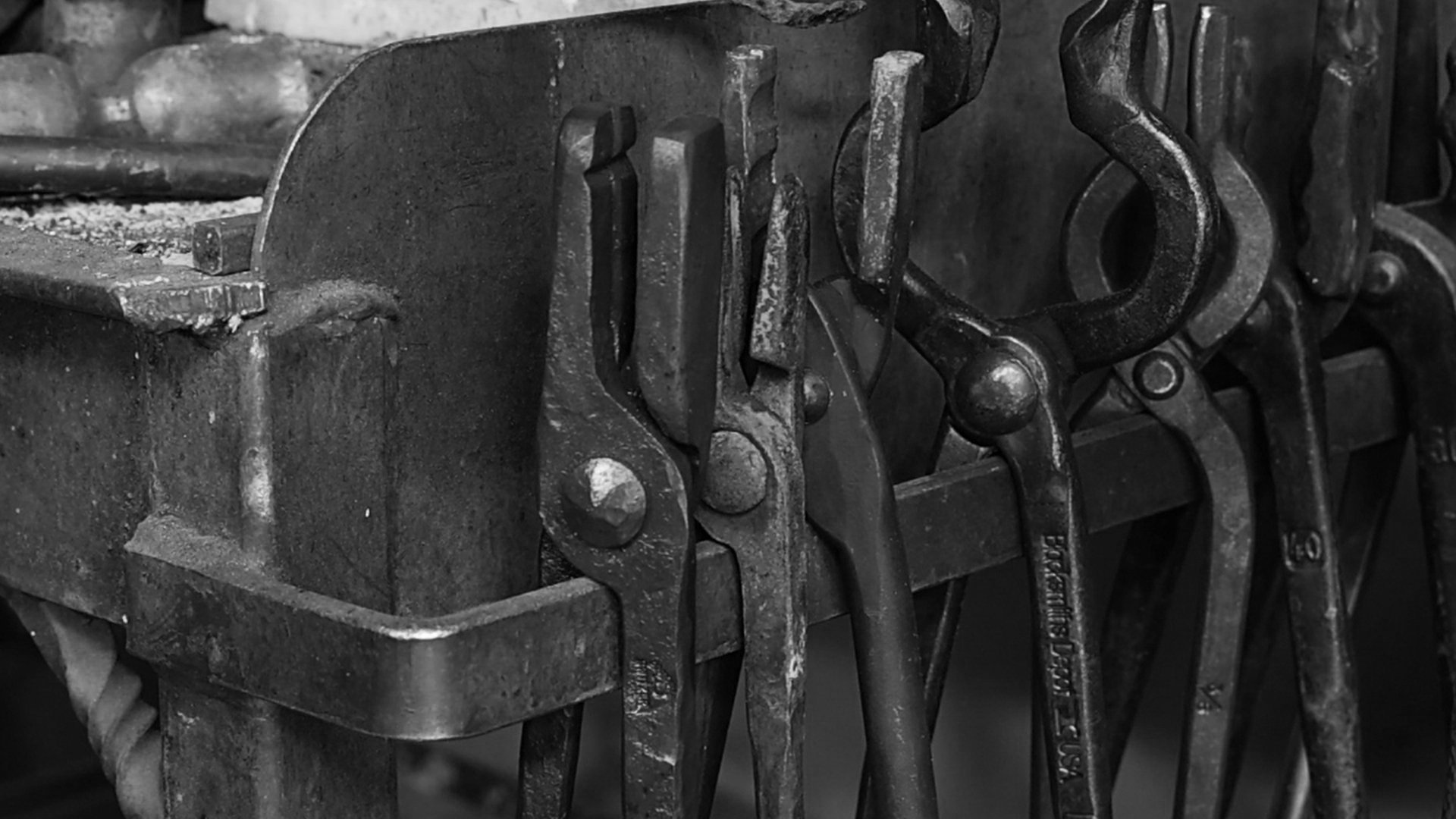
My blog
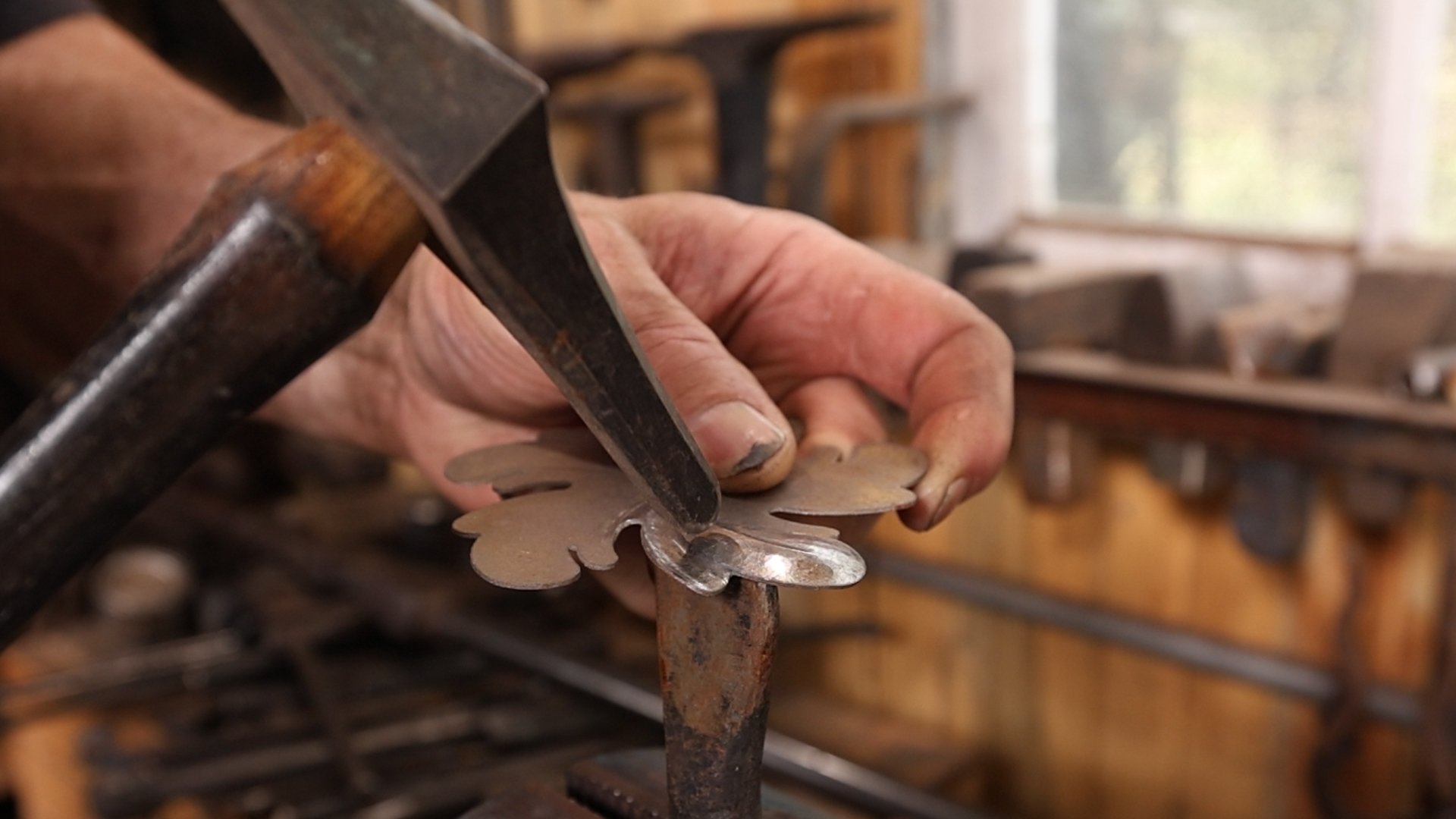
Will you call yourself a fool someday?
Is your future as a crafts person limited to skills and tools you have today? Or will you find new opportunities to learn new skills and grow in your chosen craft?
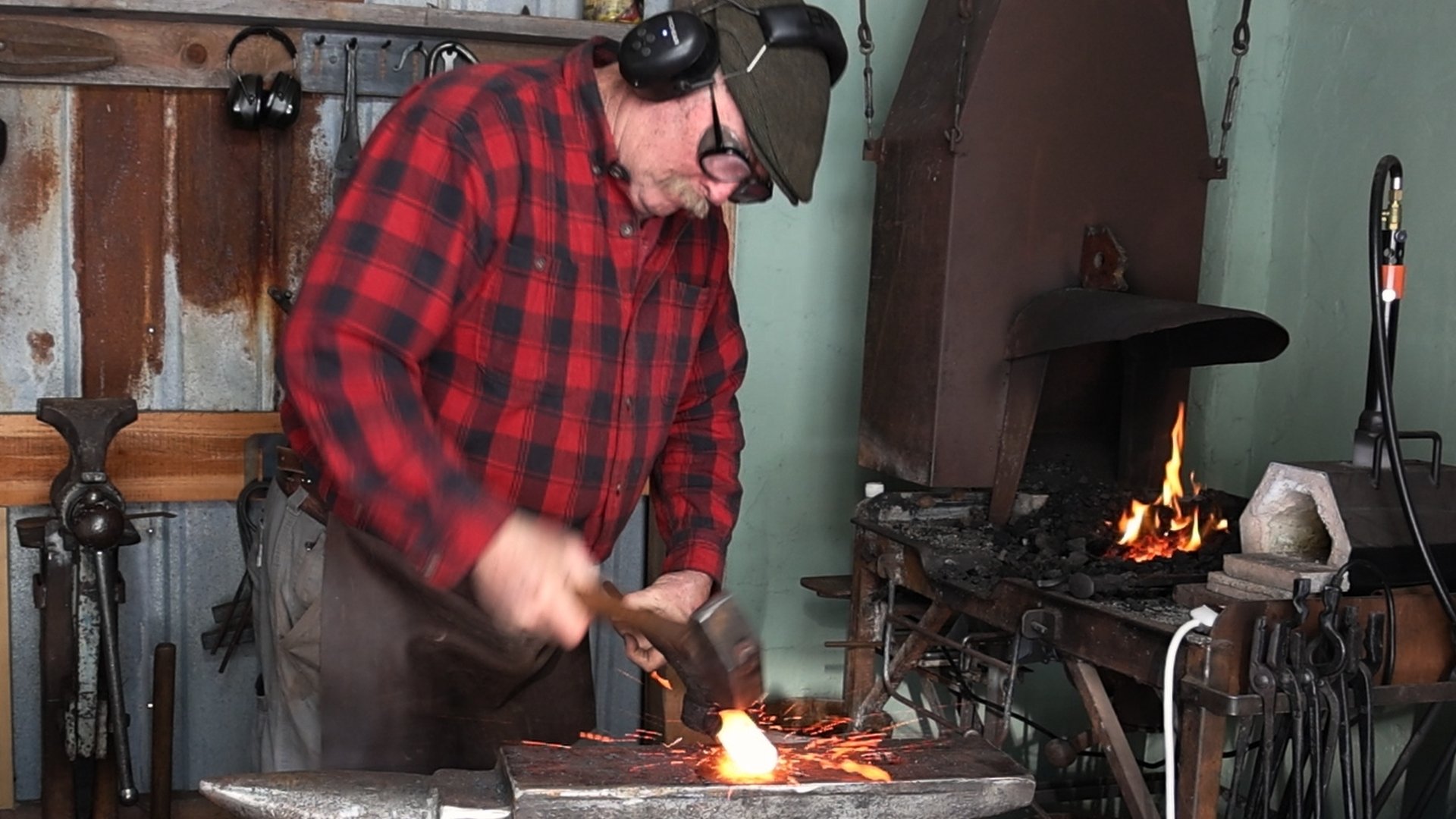
An obligation to the craft
When we participate in a craft, whether that is blacksmithing, wood carving, weaving, or so many others, do we then have an obligation to that craft? If so, what would that look like and how would we go about fulfilling that obligation? Certainly I am not talking here about a formal obligation, but rather an informal or self-imposed commitment to give back in some manner.
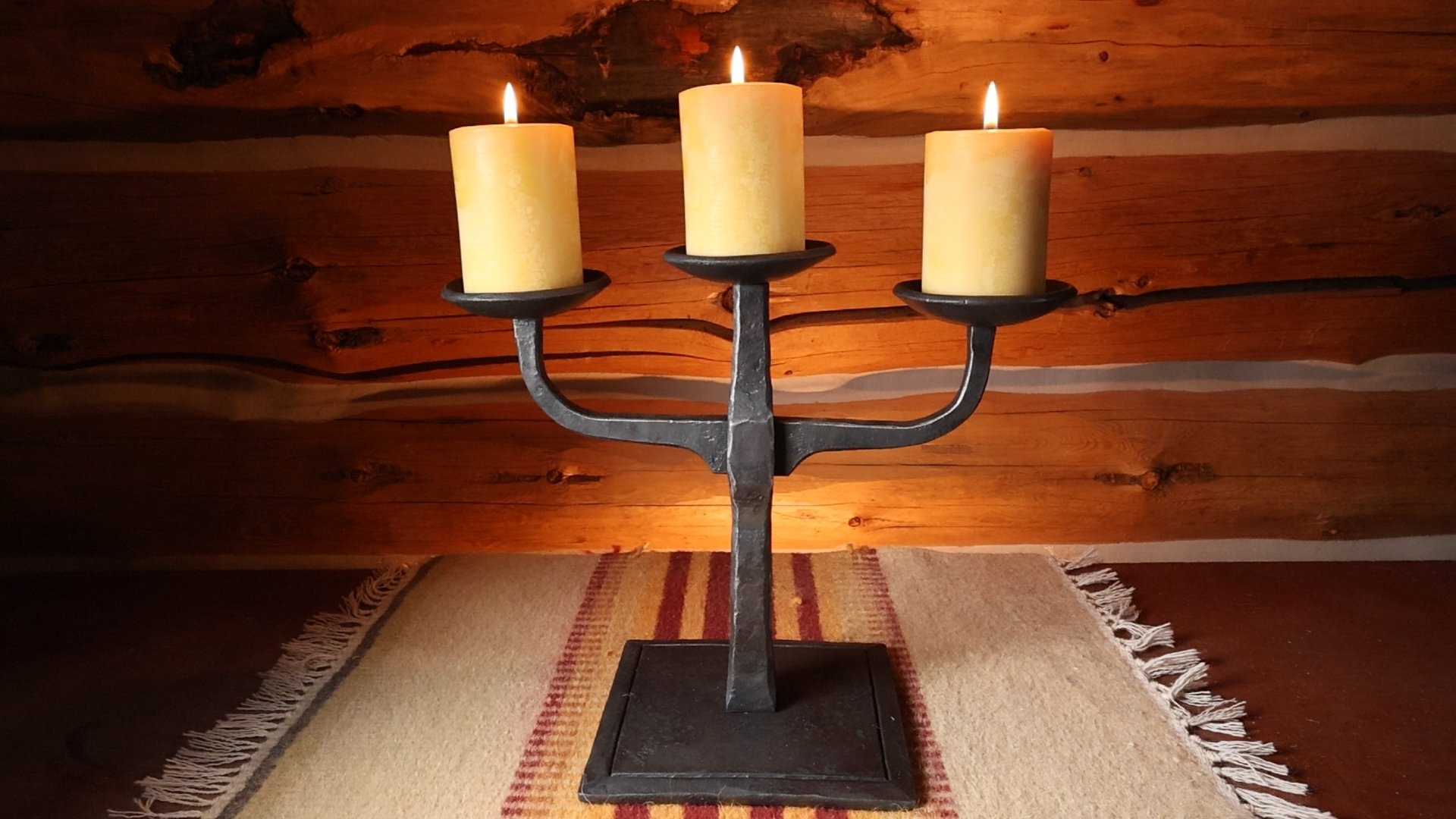
Beginning a new chapter
Sometimes the best way to challenge or improve yourself is to make a fresh start, even if it is something small